В автопроме на передовой в условиях санкций не только закупщики и логисты, которые ищут альтернативные комплектующие и выстраивают новые цепочки поставок. В конечном итоге сохранение производства зависит от профессионализма конструкторских служб, которые должны адаптировать технику к новым реалиям в рекордные сроки, сохранить модельный ряд и не остановить перспективные разработки. Объединенному инженерному центру «Группы ГАЗ» в последние годы не раз приходилось демонстрировать способность виртуозно сочетать эти процессы. А опыт нескольких поколений разработчиков и грамотная стратегия по выбору инструментов и подходов помогают быстро показывать результат.
Инструменты
Исторически так сложилось, что конструкторы ГАЗа всегда несколько опережали производственников: инженеры начали работать над первыми эскизами машин уже в 1929 году, когда сам завод, введенный в строй в 1932-м, еще только проектировался.
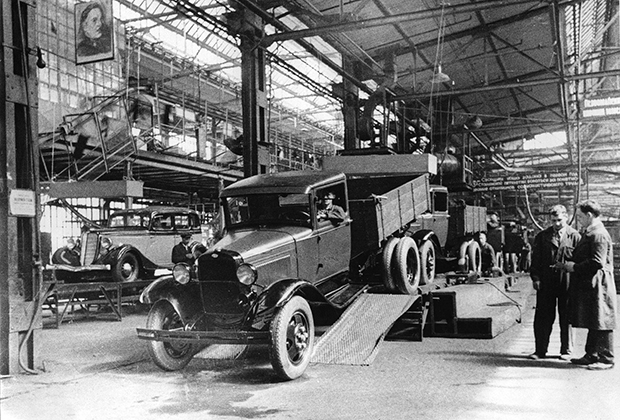
Фото музея истории ГАЗ
В начале 2000-х инженерный центр ГАЗа стал одной из первых структур нового холдинга — «Группы ГАЗ», созданного промышленником Олегом Дерипаской. Центр объединил компетенции больше десятка автомобилестроительных предприятий в нескольких регионах и стал одним из крупнейших в стране.
Изменения тогда коснулись не только формы. «До реструктуризации работали над созданием автомобиля на базе советских подходов, которые во многом не отвечали новым рыночным реалиям, поскольку формирование ключевых требований к продукции шло с уровня министерств, по сути от единого заказчика, как было принято во времена плановой экономики, — рассказывает директор по планированию продукта Объединенного инженерного центра (ОИЦ) «Группы ГАЗ» Олег Филимонов. — В новых экономических условиях мы столкнулись, с одной стороны, с необходимостью обеспечивать соответствие продукции ожиданиям сотен тысяч покупателей, а с другой — вступили в конкуренцию с мощными иностранными брендами, возможности которых по бюджету порой сопоставимы с уровнем небольшой страны».
Чтобы победить в конкуренции, действовать нужно было быстро, но при этом рационально с точки зрения затрат. «Акционер задал нам резонный вопрос: “Ребята, а кто у вас занимается продуктом с точки зрения бизнес-эффективности?” И оказалось, что комплексно — никто, у каждого своя зона ответственности. Требовалась новая модель взаимодействия подразделений Группы при создании новой продукции и современная система разработки», — продолжает Олег Филимонов. В результате одновременно с производственной системой на ГАЗе началось внедрение так называемой системы «ворот качества» — PPDS (Product Planning Development System), полностью изменившей подход к планированию и разработке продукта.
Параллельно в ходе реструктуризации компании создавались бизнес-дивизионы и Объединенный инженерный центр. «Вместе мы научились понимать логику потребителя и грамотно переводить его запросы на технический язык, разрабатывать необходимый профиль продукта, при этом обеспечивать выполнение бизнес-целей. Это большая командная работа на всех этапах — от обсуждения идеи до запуска производства, продаж, логистики», — поясняет Олег Филимонов.
В рамках проекта сначала идет работа с несколькими группами потенциальных потребителей, где определяется, какими функциями и параметрами должен обладать будущий автомобиль, устанавливаются рамки инвестиций и сроки. Потом ведется проектирование с учетом целого комплекса требований, и на каждом этапе контролируется качество и себестоимость. В результате проект превращается в матрицу, в которой у каждого своя роль, при этом все работают в рамках единых и понятных целей.
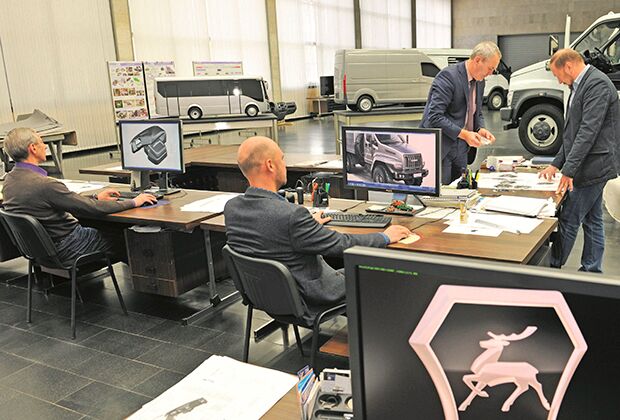
Фото: Михаил Сорокин
Создание Объединенного инженерного центра привело к важному синергетическому эффекту не только в отношении унификации технических решений, но и в соединении профессионального опыта инженеров, баз знаний в области разработки различных классов техники.
Такой комплексный подход позволил ГАЗу максимально сжать сроки разработок и быстро реагировать на любые внешние колебания улучшениями модельного ряда. Первые результаты увидели уже в 2010 году на этапе запуска «Газели Бизнес» — первого поколения машин, разработанного с новым системным подходом. В конструкцию автомобиля было внесено около 600 изменений. Бизнес-план предусматривал, что за год новое семейство займет не больше 20 процентов в продажах, а остальное по-прежнему будет за классической версией, но вышло наоборот: несмотря на разницу в цене, «Газель Бизнес» практически полностью заместила на рынке старую модель.
В 2013 году, когда в производство пошла уже «Газель NEXT», результаты снова превзошли ожидания. «Поначалу мы работали над новым поколением машин, которые должны были просто сменить “Бизнес” в рамках его рыночного позиционирования. Но уже первые опытные образцы показали, что в результате соединения инженерной школы ГАЗа и современных системных подходов сформировался автомобиль, способный конкурировать с европейскими аналогами и при этом лучше учитывающий ожидания потребителя, условия эксплуатации и параметры стоимости владения в России», — говорит Олег Филимонов.
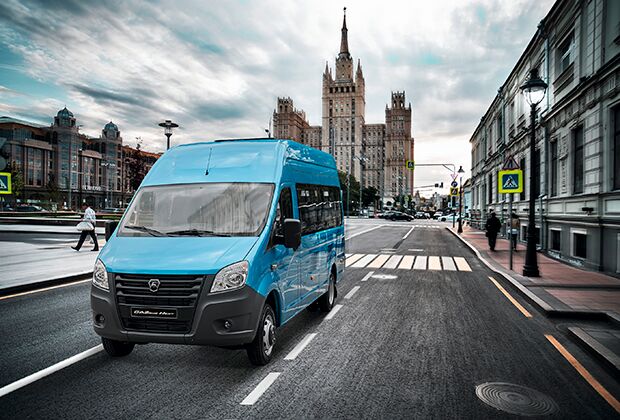
Фото: Михаил Сорокин
Новый уровень качества «Газель NEXT» подтвердили итоги аудита, проведенного экспертами двух именитых европейских испытательных лабораторий, а также специалистами известнейших мировых концернов, с которыми ГАЗ тогда налаживал проекты сотрудничества. И этот аудит явно был скрупулезным: концерны продвигали свои линейки коммерческих автомобилей на российском рынке, но ГАЗ сохранил лидерство.
Люди
Инициированные промышленником Олегом Дерипаской подходы принесли ГАЗу не только прибыль. Интенсивная работа над новыми поколениями машин требовала большого человеческого ресурса. «Именно в этот период в ОИЦ пришли молодые ребята, которые попали в очень мощную проектную среду и сразу пошли в бой», — рассказывает Олег Филимонов.
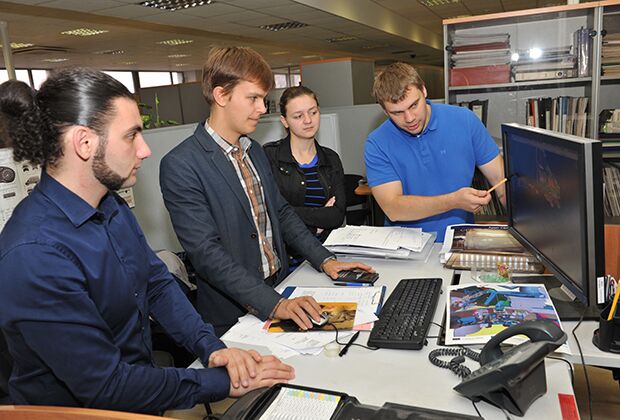
Фото: Михаил Сорокин
Он вспоминает, что так же было в начале 1990-х с ним самим — молодым специалистом, вчерашним выпускником: «Тоже было очень тяжелое время. Завод работал четыре дня в неделю, спроса практически не было, “Газель” только разрабатывалась… Но меня вовлекали во все важные проекты, со мной возились наставники разных уровней, вплоть до главного конструктора, мне доверяли реальные задачи, и так было практически с каждым молодым специалистом, который желал расти как инженер».
Сегодня на ГАЗе такие принципы работы с молодежью сохранены и развиваются, продолжает Филимонов: «Несмотря на то что загрузка опытных инженеров очень высокая, мы включаем молодых специалистов в проекты и стараемся создавать такую атмосферу, чтобы ребята могли раскрыться, проявить инициативу. Чтобы почувствовали дух творчества, дух единомышленников, который всегда был на ГАЗе».
В современную эпоху развития ГАЗа питательная инженерная среда подтянула энтузиазм вузовских научных сотрудников: за несколько последних лет были созданы мощные совместные исследовательские и конструкторские команды с МГТУ имени Баумана и НГТУ имени Алексеева.
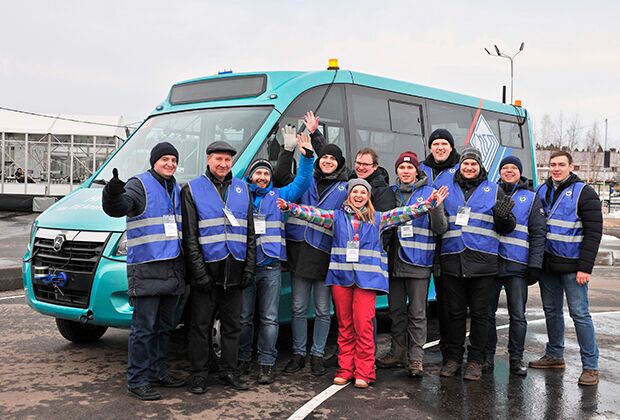
Фото: Михаил Сорокин
Безграничный полет инженерной мысли с практическим результатом — это то, чего не хватало в последние советские годы, когда инновации оставались в пределах отраслевых НИИ из-за слабого взаимодействия с промышленностью и, соответственно, недостаточного понимания реальных ожиданий предприятий.
«Конечно, мы тоже должны были созреть до необходимости заниматься исследовательскими программами в условиях, когда инженеры загружены основной проектной деятельностью и нет ясности, как вырастить и содержать команды, которые будут заниматься продуктами с неизвестной с точки зрения бизнеса перспективой», — рассказывает Олег Филимонов. Совместные проекты ГАЗа с вузами помогли раскрыть новый потенциал.
Именно благодаря такому сотрудничеству в продуктовом портфеле ГАЗа появились автомобили будущего: электромобили, водоробусы и даже беспилотники, а вместе с ними — опыт внедрения современных высокотехнологичных систем и интеллектуальных сервисов помощи водителю (ADAS-системы), которые теперь могут применяться и в серийном производстве. «Наша главная задача — обеспечить безопасность автомобиля. А один из факторов, этому способствующих, — комфортное состояние водителя во время движения, которое в машинах новых поколений обеспечивают в том числе ADAS-системы. Партнерство с учеными позволило ускорить разработку и продвижение таких технологий в серию», — комментирует Олег Филимонов.
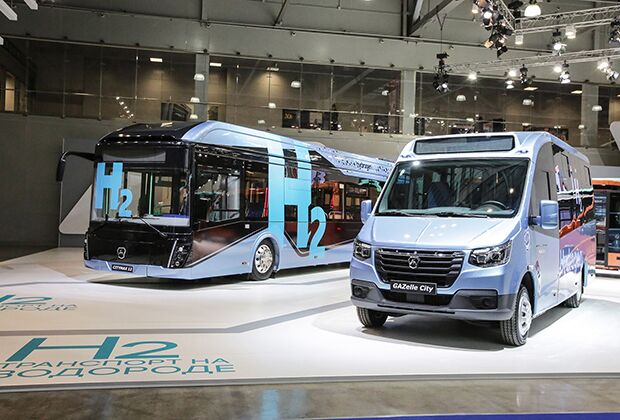
Фото: Михаил Сорокин
Подход
Смекалка инженеров, способных найти выход из любого тупика и взять из мировых практик лучшее, выручала ГАЗ во время всех кризисов последних лет, и из каждого завод выходил с новым продуктом. Один из таких примеров — создание в 2013-2014 годах среднетоннажных грузовиков нового поколения «ГАЗон NEXT». Одной из задач, которую решал инженерный центр ГАЗа, — оснащение грузовика новой кабиной, которую уже разработали для «Газели NEXT».
«Создание новой кабины — история очень затратная по вовлекаемым ресурсам специалистов, срокам и инвестициям. Задача была практически нерешаемая: заменить старую двухместную кабину на комфортное рабочее место водителя, да еще и с двумя пассажирами, сохранив при этом приемлемую себестоимость коммерческого грузового автомобиля», — рассказывает Олег Филимонов. В итоге применили кабинный модуль «Газели NEXT», со всеми его преимуществами по комфорту и унификации. Благодаря интересным конструкторским решениям и искусству дизайнеров ГАЗу удалось создать оптимальную кабину для нового среднетоннажника, который сразу после выхода на рынок стал бестселлером в своем сегменте.
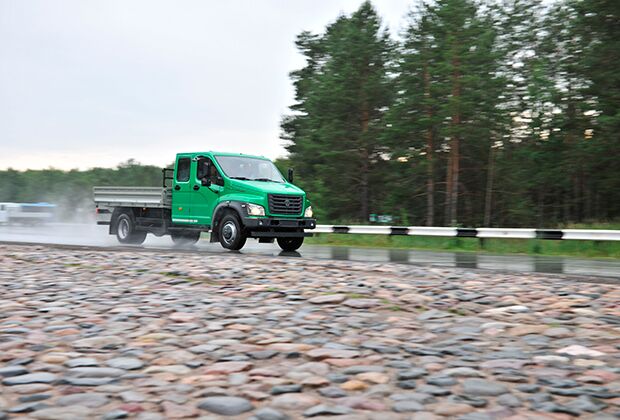
Фото: Михаил Сорокин
И это не единственный пример того, как соединение инженерной школы ГАЗа и рациональный системный взгляд обеспечивают интересные и эффективные шаги.
Унификация инженерных решений и производственных процессов, причем на всех площадках группы, — сегодня один из главных факторов роста эффективности в холдинге. Например, на шасси того же среднетоннажного «ГАЗона», который выпускается на Горьковском автозаводе, в 2016 году был создан новый автобус Павловского автобусного завода «Вектор NEXT».
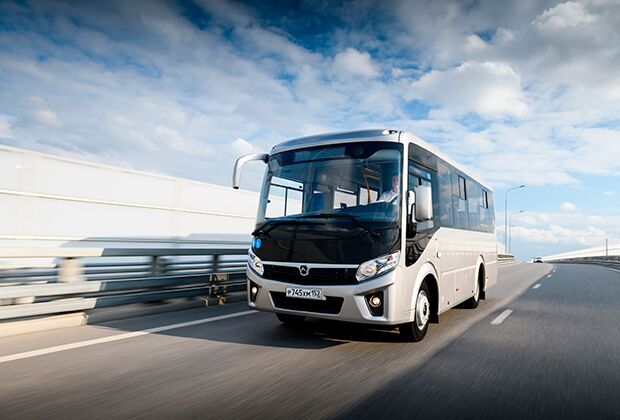
Фото: Михаил Сорокин
Передовые решения конструкторской службы ГАЗа внедряются и на зарубежных производствах «Группы ГАЗ». Так, в июне 2021 года на турецкой сборочной площадке стартовал серийный выпуск нового коммерческого автомобиля «Газель NN» с двигателем экологического класса «Евро-6». Разработке первого российского легкого коммерческого автомобиля, соответствующего такому высокому экологическому стандарту, и запуску его производства не помешали даже ограничения в период пандемии.
Этот непрестанный поиск, творческий подход всегда сопутствовали совместной работе ГАЗа с иностранными партнерами. «Если бы мы взаимодействовали бездумно, брали бы западные технологии в чистом виде, не пытаясь разобраться, в условиях ужесточающихся санкций все было бы гораздо печальнее. Но мы научились слушать, думать и разбираться во многом самостоятельно. Мы научились более эффективно формулировать требования к компонентам, когда компании требуется привлечение поставщиков, и это сейчас особенно ценно», — говорит Олег Филимонов.
Быстро реагируя на запросы рынка, даже в самые сложные годы ГАЗ не останавливал инновационное развитие. Так, в 2008-2009 годах, несмотря на глобальную финансовую нестабильность, конструкторы ОИЦ уже работали над электроплатформой, в невероятные перспективы которой тогда мало кто верил. В результате сегодня электромобили «Газель e-NN» конвейерной сборки уже работают на маршрутах в Нижнем Новгороде. А электробусы «Группы ГАЗ», которые компания производит на Ликинском автобусном заводе в Подмосковье, обслуживают пассажиров в Москве.
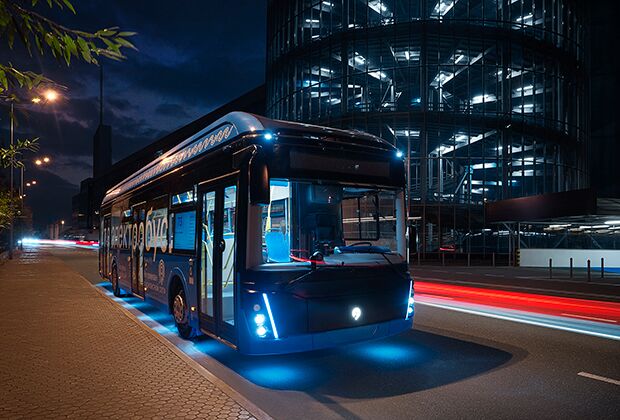
Фото: Михаил Сорокин
«Разработка нового автомобиля от идеи до конвейерного воплощения занимает не меньше пяти лет, а если речь идет о внедрении инноваций, нужно закладывать еще пять лет на исследования. С учетом того, что коммерческий транспорт — долгожитель на рынке, горизонт планирования должен быть минимум 25-летним», — говорит Олег Филимонов. Над каким транспортом будущего ОИЦ работает сейчас, инженер не раскрывает, но дал понять, что развитие не останавливается даже в беспрецедентно жестких условиях санкций.